課題内容 | 特殊・肉薄形状の実現 |
---|
効果 | コストダウン、鋳造欠陥回避 |
---|
Before (改善前)
自動車部品のオイルセパレーターの製作において、お客様より工程短縮によるコストダウン及び製造リードタイムの短縮をご要望頂き、砂型鋳造で製造することでご要望を実現した事例です。
元々当製品は鍛造とプレスでの溶接工程を経て構成されており、一般肉厚が1.5mmと肉薄であり砂型鋳造では難しいためダイキャストでの生産をお考えでしたが、小ロットであり、ダイカストでの金型製作費用が割高になってしまうことを懸念されており、砂型鋳造での製造をご要望でした。
砂型鋳造の場合、最小肉厚は2.5mm程度が限界とされ、それ以下の肉厚は、湯回り不良等発生するリスクが高く、又、湯が回ったとしても、歪抜きの際に加える応力により、クラックの発生リスクが高くなります。1.5mmを実現する為には、木型設計・工法設計の段階からの工夫が必要でした。
V
After(改善後)
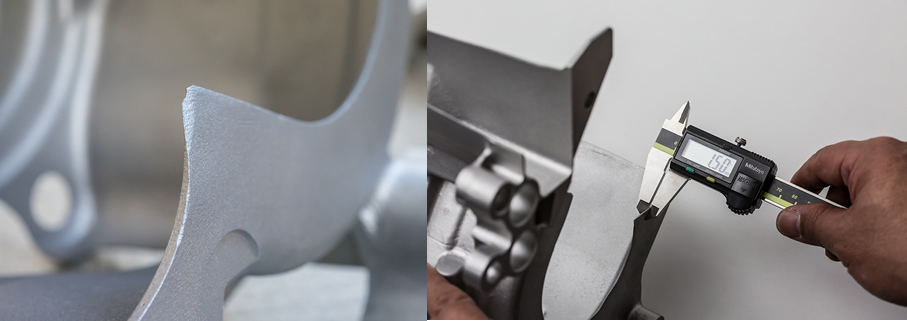
薄肉の場合、湯回り不良が発生しやすいため、鋳造解析を行うことで、湯回りを考慮した方案を検討しました。具体的には、湯流れ解析による最適なゲートの位置を検証し、凝固解析により湯回り位置やガスの発生個所を特定し、木型設計に反映しました。試鋳を重ねていくなかで、従来の重力鋳造では賄えない部分を吸引器で強制的に圧送するなど、鋳造の工法から見直すことで、肉厚1.5mmに対し湯回り不良など鋳造欠陥のない素材を製作することができました。
また、歪みの発生リスクについては、検査治具を設計・製作し歪矯正を行うだけではなく、素材非接触測定結果により歪みの傾向を元に木型に寸法補正を加えました。具体的には、非接触結果により歪での素材矯正が困難な箇所において、寸法外差分を木型へ盛り込みました。傾向として外周部の輪郭で-0.3mmほどマイナスの箇所に、+0.3mm形状を盛込む寸法補正を加えました。その結果、バラツキを抑えた、高精度な1.5mmの薄肉成型を実現しました。